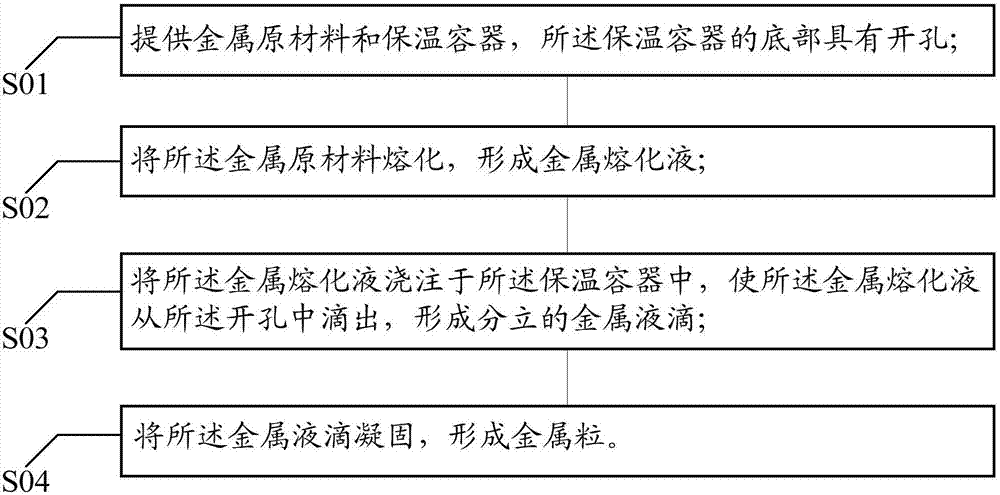
本發明涉及金屬加工領域,尤其涉及一種金屬粒的形成方法及制備金屬粒的裝置。
背景技術:
在金屬加工領域中,需要將整個金屬塊體加工成金屬粒應用于不同的領域。
如,將鋁塊體加工成鋁粒,應用于高純鋁活化直接水解法制備氧化鋁的過程中。在高純鋁活化直接水解法制備氧化鋁的過程中,采用鋁粒作為反應的原料之一,能夠增加反應接觸面積,提高反應效率。當所述氧化鋁用于純度為99.999%以上藍寶石制備時,需要使得氧化鋁的純度較高,此時需要所述鋁粒的純度也較高。
另外,在制備金屬粒的過程中,需要滿足工藝效率高的要求。
然而,現有技術形成的金屬粒的純度和金屬粒的生產效率難以同時得到保證。
技術實現要素:
本發明解決的問題是提供一種金屬粒的形成方法及制備金屬粒的裝置,以保證金屬粒的純度,且提高工藝效率。
為解決上述問題,本發明提供一種金屬粒的形成方法,包括:提供金屬原材料和保溫容器,所述保溫容器的底部具有開孔;將所述金屬原材料熔化,形成金屬熔化液;將所述金屬熔化液澆注于所述保溫容器中,使所述金屬熔化液從所述開孔中滴出,形成分立的金屬液滴;將所述金屬液滴凝固,形成金屬粒。
可選的,所述金屬原材料為鋁原材料或銅原材料。
可選的,所述金屬原材料的純度為4n5~6n。
可選的,采用熔化爐將所述金屬原材料熔化。
可選的,所述熔化爐為真空爐、電阻爐或感應爐。
可選的,當所述金屬原材料為鋁原材料時,所述熔化爐中的溫度為760攝氏度~820攝氏度。
可選的,當所述金屬原材料為銅原材料時,所述熔化爐中的溫度為1200攝氏度~1280攝氏度。
可選的,當所述金屬原材料為鋁原材料時,所述保溫容器中的保溫溫度為710攝氏度~750攝氏度。
可選的,當所述金屬原材料為銅原材料時,所述保溫容器中的保溫溫度為1150攝氏度~1200攝氏度。
可選的,所述開孔的底部開口小于等于頂部開口。
可選的,所述開孔的底部開口的尺寸為0.5mm~1mm。
可選的,相鄰開孔之間的距離至少為20mm。
可選的,所述開孔的數量為一個或多個。
可選的,將所述金屬液滴凝固的方法包括:提供收集器;將所述收集器置于所述保溫容器的下方;所述金屬液滴滴落在所述收集器中,從而凝固形成金屬粒。
可選的,所述收集器與所述保溫容器的底部表面的距離為20mm~60mm。
可選的,所述收集器為可旋轉的金屬盤或者金屬傳送帶。
可選的,還包括:對所述金屬粒進行清洗處理。
可選的,所述清洗處理的方法包括:采用異丙醇溶液或乙醇中的一種或其組合清洗所述金屬粒。
可選的,所述清洗處理的方法包括:采用硝酸與氫氟酸的混合溶液清洗所述金屬粒。
本發明還提供一種制備金屬粒的裝置,包括:熔化爐,所述熔化爐適于將金屬原材料熔化為金屬熔化液;保溫容器,所述保溫容器的底部具有開孔, 所述保溫容器適于容置所述金屬熔化液,所述開孔作為金屬融化液從保溫容器中滴落形成金屬液滴的通道;收集器,所述收集器適于將所述金屬液滴凝固為金屬粒并收集所述金屬粒
與現有技術相比,本發明的技術方案具有以下優點:
本發明將金屬原材料熔化為金屬融化液,然后將金屬融化液從保溫容器的開孔中滴落的方式形成金屬液滴,之后將所述金屬液滴冷卻形成金屬粒,避免了需要采用機械加工的方法形成金屬粒,從而避免了在形成金屬粒的過程中機械作用力作用于金屬粒;由于沒有機械作用力作用于金屬粒,一方面減少了雜質的來源,從而保證了金屬粒的純度,另一方面,降低了雜質進入金屬粒的深度,利于后續清洗,從而提高了工藝效率。
另外,金屬融化液從保溫容器的開孔中滴落可在較短的時間完成,降低了形成金屬粒需要的時間,從而提高了工藝效率。
進一步的,對所述金屬粒進行清洗處理,去除金屬粒表面的雜質,以進一步提高金屬粒的純度;同時,由于金屬粒表面的雜質較少,無需采用較多周期的重復清洗,效率較高;且由于避免了機械加工的方法形成金屬粒,少量的雜質不會嵌入金屬粒,因而降低了清洗難度。
附圖說明
圖1是本發明第一實施例中金屬粒形成過程的流程圖;
圖2至圖6是本發明第一實施例中金屬粒形成過程的實施示意圖。
具體實施方式
正如背景技術所述,現有技術中形成的金屬粒的純度和金屬粒的生產效率難以同時得到保證。
一實施例中,金屬粒的形成方法為:提供金屬原材料;依次沖壓和剪切所述金屬原材料,形成金屬粒;對所述金屬粒進行清洗。
研究發現,上述實施例中,主要采用機械加工的工藝(如沖壓和剪切工藝)形成金屬粒。在形成每個金屬粒時,機械加工工藝采用的刀具均需要和金屬原材料接觸,且機械加工工藝采用的刀具對金屬原材料產生壓力,使得 容易給金屬粒引入較多的雜質元素。由于引入的雜質元素較多,需要對金屬粒進行多次清洗,以去除雜質元素,效率較低。且生產所述金屬粒采用的機械加工工藝,如沖壓和剪切工藝均需要耗費較長的時間,進一步的降低了工藝效率。
此外,在采用機械加工工藝形成金屬粒的過程中,容易使得雜質嵌入金屬粒內,增加了清洗的難度。清洗難度增加也會增加清洗的時間。
上述實施例中,金屬粒的純度和金屬粒的生產效率難以同時得到保證。
在此基礎上,本發明提供一種金屬粒的形成方法,參考圖1,包括步驟:
步驟s01,提供金屬原材料和保溫容器,所述保溫容器的底部具有開孔;
步驟s02,將所述金屬原材料熔化,形成金屬熔化液;
步驟s03,將所述金屬熔化液澆注于所述保溫容器中,使所述金屬熔化液從所述開孔中滴出,形成分立的金屬液滴;
步驟s04,將所述金屬液滴凝固,形成金屬粒。
所述金屬粒的形成方法能夠保證金屬粒的純度,且提高工藝效率。
為使本發明的上述目的、特征和優點能夠更為明顯易懂,下面結合附圖對本發明的具體實施例做詳細的說明。
參考圖2,提供金屬原材料100。
所述金屬原材料100為后續形成金屬粒的初始材料來源,所述金屬原材料100選擇的材料根據實際需要確定。
所述金屬原材料100可以為鋁原材料或銅原材料。
所述金屬原材料100的純度大于4n5。
具體的,所述金屬原材料100的純度為5n或6n,其中,5n表示純度為99.999%,而6n表示純度為99.9999%。
參考圖3,提供保溫容器200,所述保溫容器200的底部具有開孔201。
所述保溫容器200適于后續容置金屬融化液,并使金屬融化液從開孔201中滴落。
所述保溫容器200的材料可以為碳化硅、氧化硅和氧化鋁的混合材料,使得所述保溫容器200具有耐高溫和保溫作用好的優點。
所述保溫容器200的表面還可以涂覆隔離層,所述隔離層的作用為:(1)后續金屬熔化液澆注于所述保溫容器中后,防止保溫容器200中的雜質元素進入金屬融化液中;(2)所述隔離層的表面光滑,避免金屬融化液粘附在保溫容器200的表面。
所述隔離層的材料可以為氮化硼。當后續保溫容器200容置的金屬融化液為鋁融化液時,所述隔離層的材料還可以為氧化鋁。
所述保溫容器200具有保溫溫度,使得后續金屬融化液澆注在保溫容器200中后,不會將金屬融化液凝固。
具體的,采用加熱裝置提供給保溫容器200熱量,使得保溫容器200具有保溫溫度。所述加熱裝置可以為電阻絲或液化石油氣噴燈。
所述保溫容器200的底部具有開孔201。所述開孔201作為后續金屬融化液從保溫容器200中向下滴落的通道。
所述開孔201的底部開口小于等于頂部開口。在一個實施例中,所述開孔201的底部開口小于頂部開口,所述開孔201的底部開口的尺寸為a,所述開孔201的頂部開口的尺寸為b,a小于等于b;在另一個實施例中,所述開孔的底部開口等于頂部開口。
本實施例中,所述開孔201的底部開口小于頂部開口,使得后續待形成金屬粒后,對所述保溫容器200的清洗更為方便,具體的,對開孔201的清洗更為方便。
所述開孔201的底部開口的尺寸a為0.5mm~1mm。所述開孔201的底部開口的尺寸a選擇此范圍的意義為:若所述開孔201的底部開口的尺寸a小于0.5mm,導致后續開孔201對金屬融化液造成阻塞,金屬融化液難以從開孔201中順利滴出;若所述開孔201的底部開口的尺寸a大于1mm,將導致后續金屬融化液容易從開孔201連續流出,不能形成分立的金屬液滴。
所述開孔201的數量根據實際需要進行設定。所述開孔201的數量為一 個或多個。
當所述開孔201的數量為多個時,有利于后續在不同的開孔201中同時形成金屬液滴,增加工藝的效率。
當所述開孔201的數量為多個時,相鄰開孔201之間的距離至少為20mm,好處為:由于后續金屬液滴從所述開孔201中滴落后,金屬液滴與收集器發生碰撞會引起金屬液滴變形,在平行于金屬液滴與收集器的碰撞面上,金屬液滴的尺寸會變大,容易引發從相鄰開孔201中滴落到收集器中的金屬液滴之間部分重合,難以形成分立的金屬粒;相鄰開孔201之間的距離至少為20mm,能夠有效的避免從相鄰開孔201中滴落到收集器中的金屬液滴在收集器中重合,從而避免金屬粒部分重合。具體的,相鄰開孔201之間的距離可以為20mm~40mm。
參考圖4,將所述金屬原材料100(參考圖2)熔化,形成金屬熔化液101。
本實施例中,采用熔化爐300將所述金屬原材料100熔化,具體的,將所述金屬原材料100置于熔化爐300中進行熔化,形成金屬熔化液101。
所述熔化爐300為真空爐、電阻爐或感應爐。
所述熔化爐300達到的溫度需要能夠將所述金屬原材料100熔化。若所述熔化爐300中的溫度過低,導致不能將所述金屬原材料100熔化;若所述熔化爐300中的溫度過高,導致工藝浪費,且需要提高相應的熔化爐300對溫度的承受能力。另外,考慮到后續澆注金屬熔化液101的過程中,會有部分熱量散發,而澆注后的金屬熔化液101需要具有保溫溫度,故熔化爐300中的溫度會高于保溫溫度。
綜上所述,所述熔化爐300需要選擇合適范圍的溫度,且針對不同的金屬原材料100,熔化爐300需要的溫度不同。當所述金屬原材料100為鋁原材料時,設定所述熔化爐300中的溫度為760攝氏度~820攝氏度;當所述金屬原材料為銅原材料時,設定所述熔化爐300中的溫度為1200攝氏度~1280攝氏度。
參考圖5,將所述金屬熔化液101澆注于所述保溫容器200中,使所述金屬熔化液101從所述開孔201(參考圖3)中滴出,形成分立的金屬液滴102。
所述保溫容器200的保溫溫度為保溫容器200中的金屬融化液101提供恒定的熱量,使得保溫容器200中的金屬融化液具有保溫溫度。且需要使得在澆注金屬熔化液101于保溫容器200的初始瞬間,不會將金屬熔化液101凝固而堵塞開孔201,所述保溫溫度需要至少高于金屬原材料100的熔點50攝氏度。另外,所述保溫溫度的選擇需要使得保溫容器200中的金屬熔化液101具有合適的黏度。若保溫溫度過大,導致保溫容器200中的金屬熔化液101的黏度過小,金屬熔化液101容易從開孔201中連續流出;若保溫溫度過小,導致保溫容器200中的金屬熔化液101的黏度過大,不能順利的從開孔201中滴出。再次,所述保溫溫度最高值的設定需要考慮工藝成本。
綜上所述,所述保溫溫度需要選擇合適范圍的溫度,且根據不同的金屬原材料100而設定。當所述金屬原材料100為鋁原材料時,所述保溫容器200中的保溫溫度為710攝氏度~750攝氏度,當所述金屬原材料100為銅原材料時,所述保溫容器200中的保溫溫度為1150攝氏度~1200攝氏度。
需要說明的是,當所述金屬原材料100為鋁原材料時,若保溫溫度高于750攝氏度,導致保溫容器200中的金屬熔化液101中的含氫量過高,所述金屬熔化液101中的氫元素的來源為空氣中水氣和對熔化爐300清洗后殘留的水,后續將對應形成的所述金屬液滴凝固的過程中,所述氫元素釋放,導致形成的金屬粒的內部具有大量的孔,金屬粒的形貌較差。而本實施例中,當所述金屬原材料100為鋁原材料時,將保溫容器200中的保溫溫度控制在750攝氏度以下,能夠避免金屬粒內部出現較多的氣孔,使形成的金屬粒的形貌較好。
所述金屬熔化液101能夠從所述開孔201中滴出而形成分立的金屬液滴102,一方面與所述保溫容器200中金屬熔化液101的黏度有關,另一方面與所述開孔201的底部開口的尺寸有關。而所述保溫容器200中金屬熔化液101的黏度主要由保溫容器200的保溫溫度決定,關于保溫容器200的保溫溫度與形成分立的金屬液滴102的關系在前述內容已經做出說明。關于所述開孔201的底部開口的尺寸與形成分立的金屬液滴102的關系在前述內容已經做出說明。不在詳述。
參考圖6,將所述金屬液滴102凝固,形成金屬粒103。
具體的,將所述金屬液滴102凝固的方法包括:提供收集器400;將所述收集器400置于所述保溫容器200的下方;所述金屬液滴102滴落在所述收集器400中,從而凝固形成金屬粒103。
本實施例中,形成的金屬粒103的大小可以達到2mm~12mm。
所述收集器400可以為可旋轉的金屬盤、也可以為金屬傳送帶。當所述收集器400選擇可旋轉的金屬盤或金屬傳送帶時,避免從同一開孔201中滴落的金屬粒103均落在收集器400的同一個位置,錯開從同一開孔201中滴落的金屬粒103滴落在收集器400的位置。
所述收集器400與所述保溫容器200的底部表面的距離需要選擇合適的范圍。若所述收集器400與所述保溫容器200的底部表面的距離小于20mm,導致當前滴落在收集器400中的金屬液滴102和從同一開孔201中滴落的前一金屬液滴102之間的距離過小,使得從同一開孔201中滴落在收集器400中的相鄰兩金屬液滴102之間的隔間時間過小,收集器400來不及傳送金屬液滴102凝固形成的金屬粒103,導致金屬液滴102會滴落在金屬粒103的部分表面;若所述收集器400與所述保溫容器200的底部表面的距離大于60mm,導致收集器400與所述保溫容器200的底部表面的距離過大,金屬液滴102滴落在收集器400的瞬間具有的動能過大,容易將形成的金屬粒103打碎。故本實施例中,所述收集器400與所述保溫容器200的底部表面的距離選擇為20mm~60mm。
另外,在收集器400的表面形成油膜,使得金屬粒103形成后與收集器400的粘合力較小,從而使得所述金屬粒103容易從收集器400的表面脫離。
所述油膜可以為脫膜油,如蓖麻油。
所述收集器400的材料為金屬,如不銹鋼。
另外,當連續作業凝固金屬液滴102時,收集器400的溫度可能過高,金屬液滴102凝固需要的時間較長。為了避免連續凝固金屬液滴102時導致的收集器400的溫度過高,采用冷卻裝置為收集器400進行降溫。所述冷卻裝置中的冷卻液為可以為水。
本實施例中,將金屬融化液從開孔中滴落的方法形成金屬粒,避免了需 要采用機械加工的方法形成金屬粒,從而避免了在形成金屬粒的過程中機械作用力作用于金屬粒;由于沒有機械作用力作用于金屬粒,一方面減少了雜質的來源,從而保證了金屬粒的純度,另一方面,降低了雜質進入金屬粒的深度,利于后續清洗,從而提高了工藝效率。
另外,金屬融化液從保溫容器的開孔中滴落可在較短的時間完成,降低了形成金屬粒需要的時間,從而提高了工藝效率。
第二實施例
第二實施例與第一實施例的區別在于:形成金屬粒后,對所述金屬粒進行清洗處理,以進一步的提高金屬粒的純度。
本實施例中,對所述金屬粒進行清洗處理,去除金屬粒表面的雜質,以進一步提高金屬粒的純度;同時,由于金屬粒表面的雜質較少,無需采用較多周期的重復清洗,效率較高;且由于避免了機械加工的方法形成金屬粒,少量的雜質不會嵌入金屬粒,因而降低了清洗難度。
具體的,采用清洗液對金屬粒進行清洗處理。
若金屬粒接觸到油污染物,如油膜材料,需要去除金屬粒表面接觸到油污染物,采用的清洗液為醇類有機物溶液,如異丙醇溶液、乙醇溶液或者其組合,所述異丙醇溶液中異丙醇的質量百分比濃度為99.99%,所述乙醇溶液中乙醇的質量百分比濃度為99.99%。
若金屬粒表面具有金屬雜質,采用的清洗液可以為硝酸與氫氟酸的混合溶液,能夠去除金屬雜質,硝酸的體積百分比濃度為2%~8%,氫氟酸的體積百分比濃度為0.5%~1%。
在一個具體的實施例中,所述清洗處理的方法為:依次采用自來水、異丙醇溶液、硝酸與氫氟酸的混合溶液、以及純水清洗所述金屬粒。
采用所述自來水清洗金屬粒,能夠潤濕金屬粒的表面,對金屬粒進行預清洗;采用純水清洗金屬粒,將殘余在金屬粒表面的異丙醇、硝酸與氫氟酸去除。
所述清洗處理采用的工藝可以為氣體噴射工藝。
所述氣體噴射工藝指的是:通過氣泵給予清洗液動力,且在清洗液流動的管道前端的噴頭中具有通入高壓氣體的通道,將高壓氣體通過所述通道施加給所述清洗液,將所述清洗液噴射在金屬粒表面,使得所述清洗液對金屬粒表面產生高的沖擊力。氣體噴射工藝采用的高壓氣體可以為n2,n2的流量可以為4000sccm~80000sccm。
所述清洗處理采用的工藝也可以為:將金屬粒放置于清洗液中,采用攪拌的方式使金屬粒和清洗液充分接觸,以達到清洗的目的。
第三實施例
本實施例提供一種制備金屬粒的裝置,包括:熔化爐300(參考圖4),所述熔化爐300適于將金屬原材料熔化為金屬熔化液;保溫容器200(參考圖3),所述保溫容器200的底部具有開孔201(參考圖3),所述保溫容器200適于容置所述金屬熔化液,所述開孔201作為金屬融化液從保溫容器200中滴落形成金屬液滴的通道;收集器400(參考圖6),所述收集器400適于將所述金屬液滴凝固為金屬粒并收集所述金屬粒。
關于所述熔化爐300、保溫容器200和收集器400的說明參照第一實施例,不再詳述。
雖然本發明披露如上,但本發明并非限定于此。任何本領域技術人員,在不脫離本發明的精神和范圍內,均可作各種更動與修改,因此本發明的保護范圍應當以權利要求所限定的范圍為準。