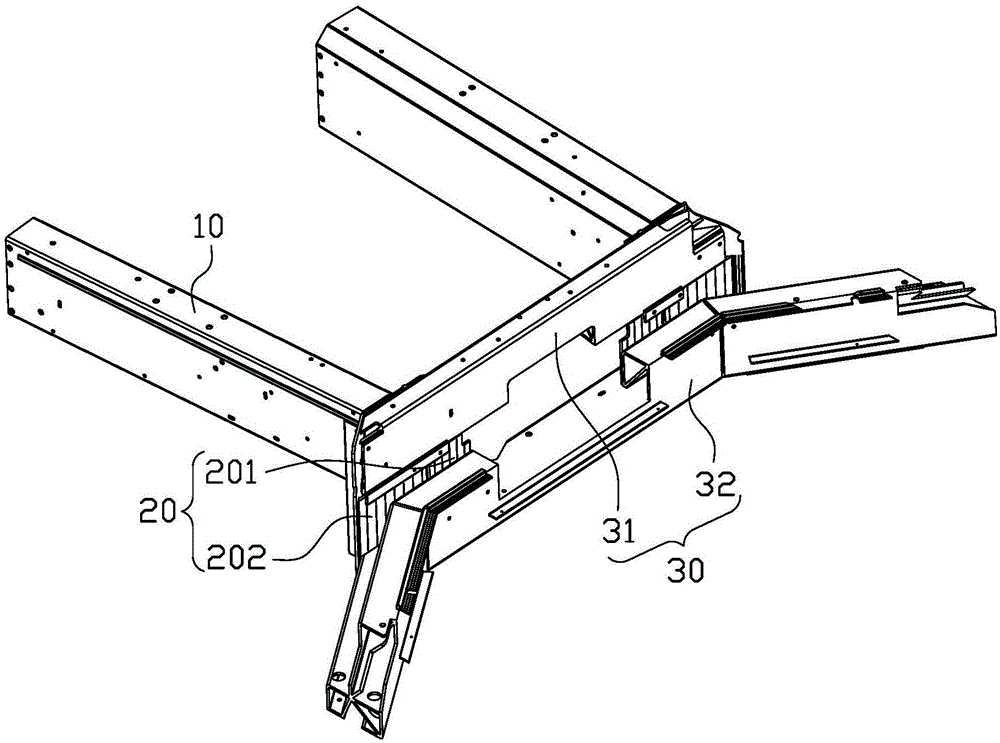
本發明涉及一種汽車零部件之間的連接結構,特別涉及一種汽車機艙縱梁與前圍橫梁的連接結構。
背景技術:
目前,市場上全鋁車身技術越來越普及,全鋁車身車型的機艙縱梁與橫梁的連接主要有鋁板沖壓零件相互搭接或型材零件與鑄鋁零件搭接兩種連接方式。鋁板沖壓零件相互搭接的形式,該結構組成零件較多且均沖壓成型,縱梁與橫梁均通過零件翻邊點焊、焊接或鉚接等形式連接。而型材零件與鑄鋁零件搭接形式,主要零部件為型材縱梁以及鑄鋁零件,兩者主要通過鉚接或焊接進行連接。
其中,鋁合金零件沖壓模具成本基本上在100萬到200萬不等,而型材零件模具成本只有1-4萬。鋁鑄件結構復雜,設計周期長、模具成本高,存在不可見的鑄造缺陷等缺點。如采用焊接這種連接方式,焊接存在較大面積的熱影響區,導致熱影響區材料性能降低30%-40%,而且焊接對零件的變形方向存在不確定性,這將導致車身制造精度降低。鉚接的連接方式,存在剪切強度低、剝離強度低的缺點。
技術實現要素:
有鑒于此,本發明旨在提出一種汽車機艙縱梁與前圍橫梁的連接結構,以克服傳統的連接結構零件模具開發成本高、零部件剛度及強度差、連接強度低、焊接影響區大、焊接工藝要求高、制造精度低的技術問題。
本發明提供的汽車機艙縱梁與前圍橫梁的連接結構,所述汽車機艙縱梁包括兩個位于汽車兩側且沿汽車前后方向延伸的機艙縱梁總成,兩個機艙縱梁總成的后端之間連接前圍橫梁,該兩機艙縱梁總成分別通過一連接結構與所述前圍橫梁固定連接,該連接結構的前端與所述機艙縱梁總成左右兩側面膠接,該連接結構后端與所述前圍橫梁膠接。
進一步地,所述連接結構前端設有相互平行的第一膠接面與第二膠接面,該第一膠接面與第二膠接面與所述機艙縱梁總成左右兩側面膠接。
進一步地,所述連接結構后端還設有與所述前圍橫梁連接的第三膠接面與第四膠接面,該第三膠接面與第四膠接面相互平行設置。
進一步地,所述第三膠接面與第四膠接面呈階梯狀,所述第三膠接面設在所述第四膠接面左右兩側呈凸字形結構,所述第四膠接面遠離所述機艙縱梁總成。
進一步地,所述第一膠接面、第二膠接面與所述第三膠接面相互垂直,所述第一膠接面、第二膠接面與所述第四膠接面相互垂直。
進一步地,該連接結構包括第一連接件與第二連接件,該第一連接件上設有一鉸接部,所述鉸接部內部還設有一弧形凹槽,該第二連接件一端設有與所述弧形凹槽形狀相適配的凸塊,該凸塊可嵌入該弧形凹槽內,該第二連接件可以該凸塊為旋轉中心旋轉。
進一步地,該第一連接件與第二連接體上均設有一粘接面,所述第二連接件通過該凸塊嵌入該鉸接部內旋轉,使該兩粘接面相互貼合。
進一步地,所述第一膠接面、第二膠接面、第四膠接面、以及第一連接件與第二連接件上的粘接面上均設有涂膠槽。
進一步地,所述前圍橫梁包括前圍上橫梁與前圍下橫梁,該前圍上橫梁與前圍下橫梁呈階梯式結構。
進一步地,所述前圍上橫梁與位于第四膠接面上側的第三膠接面膠接,位于第四膠接面下側的第三膠接面與所述前圍下橫梁膠接,所述第四膠接面上側與前圍上橫梁膠接,所述第四膠接面下側與所述前圍下橫梁膠接。
本發明的汽車機艙縱梁與前圍橫梁的連接結構,機艙縱梁與前圍橫梁采用擁有較好的剛度及強度鋁合金型材,且型材模具投入成本低,生產效率高。該連接結構結構新穎獨特,實現縱梁與橫梁的立體連接,采用結構膠粘接工藝,因結構膠冷粘接熱固化的特性,使得粘接區域無熱影響區,粘接固化后的強度不受影響。同時,在結構膠未固化之前利用其膠厚度消除零件自身制造誤差以及零件之間的裝配偏差,從而提高制造精度。
附圖說明
圖1為本發明汽車機艙縱梁與前圍橫梁的連接結構的立體結構示意圖。
圖2為圖1中的分解結構示意圖。
圖3為機艙縱梁與連接結構連接裝配示意圖。
圖4為機艙縱梁與連接結構的裝配過程的剖面示意圖。
圖5為機艙縱梁與連接結構裝配完成后的剖面示意圖。
圖6為前圍上橫梁的結構示意圖。
圖7為前圍下橫梁的結構示意圖。
具體實施方式
為更進一步闡述本發明為達成預定發明目的所采用的技術手段及功效,以下結合附圖及較佳實施例,對本發明的具體實施方式、結構、特征及其功效,詳細說明如后。
如圖1、圖2所示,一種汽車機艙縱梁與前圍橫梁的連接結構,所述汽車機艙縱梁包括兩個位于汽車兩側且沿汽車前后方向延伸的機艙縱梁總成10,兩個機艙縱梁總成10的后端連接一前圍橫梁30,該兩機艙縱梁總成10分別通過一連接結構20與所述前圍橫梁30固定連接,該連接結構20的前端與所述機艙縱梁總成10左右兩側面膠接,該連接結構20后端與所述前圍橫梁30膠接。
如圖2及圖4所示,該連接結構20包括第一連接件201與第二連接件202,該第一連接件201上設有一鉸接部25,該鉸接部25內部還設有一弧形凹槽26,該第二連接件202一端設有與所述弧形凹槽26形狀相適配的凸塊27,該凸塊27可嵌入該弧形凹槽26內,該第二連接件202能夠以該凸塊27為旋轉中心旋轉。
具體地,所述連接結構20前端設有第一膠接面21與第二膠接面22,其中,該第一膠接面21位于該第一連接件201上,該第二膠接面22設在該第二連接件202上,該第一膠接面21與第二膠接面22相對且平行設置在該機艙縱梁總成10左右兩側。該第一膠接面21與第二膠接面22與所述機艙縱梁總成10左右兩側面通過結構膠連接。
該連接結構20后端還設有與所述前圍橫梁30連接的第三膠接面23與第四膠接面24,該第三膠接面23與第四膠接面24相互平行設置。所述第三膠接面23與第四膠接面24呈階梯狀,所述第三膠接面23設在所述第四膠接面24上下兩側呈凸字形結構,所述第四膠接面24遠離所述機艙縱梁總成10。
可以理解的,所述第一膠接面21、第二膠接面22與所述第三膠接面23相互垂直,所述第一膠接面21、第二膠接面22與所述第四膠接面24相互垂直。
其中,該第一連接件201與第二連接件202上均設有一粘接面(圖未標號),所述第二連接件202通過該凸塊27嵌入該鉸接部25內,并沿圖4中箭頭所示方向旋轉,使兩粘接面相互貼合,該第一膠接面21與第二膠接面22平行且均與所述機艙縱梁總成10左右兩側面貼合(如圖5所示)。
為保證膠接區域的連接強度,在所述第一膠接面21、第二膠接面22、第四膠接面24、以及第一連接體201與第二連接體202的粘接面上均設有涂膠槽(圖未標號),在本實施例中,該涂膠槽的深度為0.2mm,使膠接區域擁有足夠的結構膠,且明確作用區域。
如圖2、圖6及圖7所示,所述前圍橫梁30包括前圍上橫梁31與前圍下橫梁32,該前圍上橫梁31與前圍下橫梁32呈階梯式結構。該第三膠接面23位于該第四膠接面24上側部分與所述前圍上橫梁31膠接,該第三膠接面23位于該第四膠接面24下側部分與所述前圍下橫梁32連接。該第四膠接面24的上側與所述前圍上橫梁31膠接,其下側部分與前圍下橫梁32膠接。
圖4為機艙縱梁與連接結構的裝配過程的剖面示意圖,其裝配過程如圖4所示,先在第一連接件201的第一膠接面21上涂敷結構膠并與所述機艙縱梁總成10的右側面粘接裝配,第二連接件202一端的凸塊27嵌入到該第一連接件201的鉸鏈部25中,該鉸接部25內部以及第二膠接面22上事先涂敷有結構膠,接著,該第二連接件202沿圖4中箭頭方向旋轉,直至第二連接件202上的第二膠接面22與機艙縱梁總成10的左側面粘接裝配,裝配完畢后的狀態如圖5所示。
應當理解的,該鉸接部25內部也涂敷結構膠,能夠防止零件裝配后出現異響。該第一連接件201與第二連接件202相貼合的粘接面同樣采用結構膠粘接連接。
接著,進行與前圍橫梁30的裝配,因前圍橫梁30分為前圍上橫梁31與前圍下橫梁32,且該前圍上橫梁31與前圍下橫梁32采用前后階梯式結構,與連接結構20粘接后能夠實現立體連接。具體地,先在第三膠接面23與第四膠接面24上涂敷結構膠,該第三膠接面23位于該第四膠接面24上側部分與所述前圍上橫梁31膠接,該第三膠接面23位于該第四膠接面24下側部分與所述前圍下橫梁32連接。該第四膠接面24的上端與所述前圍上橫梁31膠接,其下側部分與前圍下橫梁32膠接。
需要說明的是,本發明中使用的結構膠,其常溫下為稠狀流體,加熱到一定溫度后保持一段時間即可充分固化,其固化溫度較低,與焊接相比無熱影響區,即粘接區域零件的強度不受影響,等同于母材。本實施例中所采用的結構膠,在加熱到190°后保持30分鐘即可充分固化。也就是說,可在結構膠未固化前利用結構膠厚度消除零件自身制造偏差以及零件之間的裝配誤差,達到提高制造精度的目的。
本發明中,機艙縱梁總成10與前圍橫梁30均采用性能較好的鋁合金型材,型材內部晶粒更細,因而具有較好的強度及剛度,另外,鋁合金型材模具的成本也較低,使得本發明的模具成本大大降低,同時也可提高生產效率。
綜上所述,本發明的汽車機艙縱梁與前圍橫梁的連接結構,機艙縱梁與前圍橫梁采用擁有較好的剛度及強度的鋁合金型材,且型材模具投入成本低,生產效率高。該連接結構結構新穎獨特,實現縱梁與橫梁的立體連接,采用結構膠粘接工藝,因結構膠冷粘接熱固化的特性,使得粘接區域無熱影響,粘接固化后的強度不受影響。同時,在結構膠未固化之前利用其膠厚度消除零件自身制造誤差以及零件之間的裝配偏差,從而提高制造精度。
本文應用了具體個例對本發明的汽車機艙縱梁與前圍橫梁的連接結構及實施例進行了闡述,以上實施方式的說明只是用于幫助理解本發明的方法及其核心思想;同時,對于本領域的一般技術人員,依據本發明的思想,在具體實施例及其應用范圍上均會有改變之處,綜上,本說明書內容不應理解為對本發明的限制,本發明的保護范圍應以所附的權利要求為準。